Теория механизмов и механика машин
Задание № 143*. Проектирование механизмов
трехподвижного уравновешенного манипулятора
Сбалансированный манипулятор (рис. 143) используется как грузоподъемная машина для подъема (рис. 143, б) и горизонтального перемещения (рис. 143, а) изделий. Он содержит систему уравновешивания рабочего органа при перемещении в пределах зоны обслуживания. Такие манипуляторы позволяют легко перемещать изделия по желаемой траектории Тр.Е (рис. 143, а, б, в) с регулируемым изменением скорости VE(SE) перемещения (рис. 143, г). Система уравновешивания содержит автоматические пневматические устройства на базе командаппарата и не допускает произвольного смещения груза по горизонтали и предотвращает свободное падение груза при аварийных ситуациях в системе управления.
Сбалансированный манипулятор имеет приводы вертикального Да (см. рис. 143, б) и горизонтального Дс (см. рис. 143, а) перемещений и поворота звена 5 вокруг вертикальной оси y Дy. Управление приводами осуществляется вручную с помощью рукоятки управления или устройствами задания программного движения с разделением движений по различным подвижностям во времени.
Структурные схемы манипуляционного механизма с тремя степенями свободы и механизма подачи изделий в начальную позицию Енач представлены на рис. 143, в, д. Пантограф можно рассматривать как схему базового плоского механизма ABDCFE с двумя степенями свободы W=2, устанавливаемого на поворотной платформе 5 (см. рис. 143, д), приводящейся в движение от электрического двигателя Дy с помощью рядовой зубчатой передачи z1, z2 (b = 0) и планетарного редуктора ПР. Торможение осуществляется соответствующими тормозами двигателей. Оси A, B,C, D, F звеньев механизма пантографа параллельны. Соответственно параллельны осевые линии звеньев 1 и 4, 2 и 3.
При движении груза по вертикали рабочая точка C горизонтального привода Дс остается неподвижной (см. рис. 143, б), а точка А
изменяет положение с помощью привода вертикального перемещения Да. При движении точки Е
схвата в горизонтальной плоскости неподвижной является точка А (см.
рис. 143, а), а точка С изменяет положение с помощью привода горизонтального перемещения Дс. При движении по другим траекториям должны работать оба привода Да и Дс одновременно.
Уравновешивание манипулятора осуществляется с помощью пневматического привода, давление в котором поддерживается при работе с помощью автоматического устройства.
Управление подъемом груза начинается с уравновешивания манипулятора посредством увеличения давления в пневматическом цилиндре уравновешивающего устройства (на схеме не показано) до отрыва груза. После этого давление в пневмосистеме поддерживается постоянным и в действие вступают последовательно приводы вертикального и горизонтального перемещений или поворота. Торможение осуществляется автоматически после перевода системы управления в соответствующий режим. Уравновешивание груза при этом не нарушается. Выключение системы уравновешивания производится после остановки манипулятора.
Законы движения изделия из накопителя в позицию Енач при горизонтальном перемещении толкателя кулачкового механизма показаны на рис. 8.6 в пособии [1]. Исходные данные на проектирование кулачкового механизма (см. рис. 143, д) приведены в табл. 8.1 пособия [1]. Варианты структурных схем манипулятора показаны на рис. 143, а, б, в. Варианты программного движения груза по траектории (см. рис. 143, г) представлены в табл. 8.1 пособия [1].
Основные этапы проектирования
1. Проектирование кинематической схемы и определение размеров звеньев.
2. Решение прямой задачи кинематики механизма манипулятора, определение передаточных отношений, положений, скоростей и ускорений точек по соответствующим обобщенным координатам.
3. Уравновешивание манипулятора в нижнем положении. Определение реакций в кинематических парах основного механизма при максимальных ускорениях груза.
4. Динамическое исследование по определению зависимости необходимой движущей силы для воспроизведения заданного закона подъема груза.
5. Определение момента отключения двигателя и перехода в режим торможения при повороте, закона движения и оптимального передаточного отношения планетарного редуктора по критерию быстродействия.
6. Расчет рядовой зубчатой передачи и планетарного механизма. Проектирование планетарного механизма провести по согласованию с преподавателем.
7. Проектирование кулачкового механизма.
Основные результаты расчета следует приводить в пояснительной записке формата А4, графическую информацию — на четырех листах формата А1:
1-й лист - уравновешивание манипулятора;
2-й лист - динамическое исследование;
3-й лист - зубчатые передачи;
4-й лист - кулачковый механизм.
Примечание к расчету
Взаимосвязь вертикального и горизонтального перемещений схвата манипулятора основана на свойстве пантографа, по которому три его точки А, С, Е при любом положении механизма находятся на одной прямой. Для упрощения динамического расчета вспомогательные звенья, служащие для уравновешивания, не учитываются. В качестве примера рассмотрим пантограф (см. рис. 143, в). Передаточным отношением пантографа uП является отношение скоростей схвата и точки начального звена. Например, для вертикального движения (см. рис. 143, б)

Из подобия треугольников ADE и ABC; ADE и CFE следует, что

поэтому передаточное отношение механизма пантографа uп=VE /VA постоянно; его называют коэффициентом K пантографа.
Аналогичные движения происходят при постоянном положении точки А и перемещении точки С начального звена 6 по горизонтали (см. рис. 143, а). При проектировании часто принимают uп =
= 5 - 10, а длину DF, равной половине максимального перемещения схвата.
Т а б л и ц а 143.1
Исходные данные для проектирования
№ п/п |
Величина |
Обозначение |
Числовое значение |
1 |
Мощность двигателя привода Ду поворота платформы при n=1500 об/мин |
Р |
2,5 кВт |
2 |
Грузоподъемность |
mЕ |
270 кг |
3 |
Линейная плотность по длине звеньев |
r |
2,40 кг/м |
4 |
Максимальная высота подъема груза |
HE |
1100 мм |
5 |
Угол оси поворота платформы 5 вокруг вертикальной оси |
j |
180° |
6 |
Максимальная скорость подъема груза |
VE max |
3,3 м/c |
7 |
Максимальное ускорение груза |
аE max |
10 м/с2 |
8 |
Отношение тормозного момента к движущему |
KM |
2 |
9 |
Передаточное отношение прямозубой рядовой зубчатой передачи |
u12=z2/z1 |
1,5 |
10 |
Число зубьев шестерни |
z1 |
10 |
11 |
Модуль зубчатых колес z1 и z2 |
m |
4 мм |
12 |
Максимальный допустимый угол давления в кулачковом механизме |
J |
30° |
13 |
Ход толкателя кулачкового механизма |
HИ |
0,01 м |
14 |
Рабочий угол профиля кулачка |
j1р |
180° |
Т а б л и ц а 143.2
Варианты заданий, определяющие условия
перемещения груза по заданной траектории
№ |
Исходные данные |
Варианты |
||||
п/п |
А |
Б |
В |
Г |
Д |
|
1 |
Номер графика ускорений при перемещении схвата по пособию [1] |
15 |
14 |
13 |
12 |
4 |
2 |
Коэффициенты графика: K1 K2 |
0,3 0,5 |
0,4 0,6 |
0,4 0,4 |
0,5 0,5 |
0,3 0,5 |
3 |
Коэффициент пантографа Uп=CE/CA |
4,0 |
4,5 |
5,0 |
4,2 |
5,5 |
4 |
Угол bE
наклона траектории к оси x, град |
90 |
80 |
70 |
85 |
60 |
5 |
Высота подъема схвата по оси y, мм |
1000 |
800 |
900 |
1050 |
950 |
6 |
Предельное значение ускорения схвата при подъеме аE max, м/с2 |
4 |
8 |
8,5 |
4,5 |
9 |

Рис. 143
Задание № 144. Проектирование и исследование
механизма опорного устройства
Опорное устройство служит для установки изделия перед использованием.
Опоры - автономные, гидравлические связи опор обеспечивают синхронность их функционирования при установке изделия.
Структурная схема одной опоры (рис. 144, а) представляет собой плоский двухкоромысловый четырехшарнирный механизм, размеры которого определяются соотношениями: lAD = 0,5lAB; lAK =
= 0,2lAB; lKN = lAB; lAM =1,2lAB.
Механизм опоры фиксируется под нагрузкой замком (на рисунке не показан) таким образом, чтобы обеспечить условие параллельности звеньев AD и BC. При сходе изделия замок освобождается, отвод опоры осуществляется под воздействием противовеса П, укрепленного на звене 1, массу которого следует определить. В конце рабочего хода механизма (при j1 = j1 кон) положение противовеса должно определяться условием yПкон = 0.
Воздействие изделия на опору определяется силой FM, изменяющейся в зависимости от величины угла j1 по закону, представленному на рис. 144, а.
Торможение опоры осуществляется гидробуфером 4 с момента, когда j1 = j1 нач + 20°, обеспечивая ее безударный останов.
При установке опоры в исходное положение используется зубчатый механизм, состоящий из планетарного редуктора с числами зубьев колес z1 , z2 , z3 , z4 (рис. 144, б), передаточное отношение которого u1H, и зубчатой передачи с числами зубьев колес z5 и z6 .
Общее передаточное отношение зубчатого механизма u16.
Смазка подвижных соединений опор осуществляется с помощью масляного насоса кулачкового типа (рис. 144, в), состоящего из дискового кулачка 6 и плунжера (толкателя) 7. Закон изменения скорости толкателя в зависимости от угла поворота кулачка представлен на рис. 144, в.
Исходные данные для проектирования приведены в табл. 144.
Задание на проектирование - в соответствии с учебным планом.
П р и м е ч а н и я:
1. При определении закона движения механизма расчеты проводить с интервалом изменения угловой координаты звена 1 Dj1 = 5°. Конечное значение угловой координаты j1 кон необходимо вычислить.
2. Приведенный момент от силы сопротивления гидробуфера

3. Учет трения в кинематических парах механизма выполнить условно, считая суммарный приведенный момент от сил трения постоянным и равным


4. Массу противовеса считать сосредоточенной в точке N и определить из условия, что в начальный момент времени приведенный момент от силы тяжести противовеса обеспечит соотношение



5. Центры масс звеньев рычажного механизма расположены посередине длин звеньев. Моменты инерции звеньев относительно осей, проходящих через их центры масс, считать по формуле

6. При проектировании зубчатого редуктора модуль зубчатых колес редуктора принять одинаковым. Угол наклона линии зуба зубчатых колес b = 0.
7. При проектировании рабочего профиля кулачка угловую скорость кулачка принять равной максимальному значению угловой скорости звена 1 w кул = w1 max . Угол рабочего профиля кулачка dр = j1 кон, допустимый угол давления [J] = 30°.
Т а б л и ц а 144
Исходные данные для проектирования
№ п/п |
Величина |
Еди-ница |
Числовые значения величин для вариантов |
||||
изме-рения |
А |
Б |
В |
Г |
Д |
||
1 |
Длина звена 1 lАВ |
м |
3,0 |
3,1 |
2,9 |
2,8 |
3,2 |
2 |
Угловая координата звена 1 в начальном положении опоры j1 нач |
град |
60 |
60 |
60 |
60 |
60 |
3 |
Угловая координата звена 3 в начальном положении опоры g3 нач |
град |
100 |
100 |
100 |
100 |
100 |
4 |
Максимальное значение усилия FM
max |
Н |
2×105 |
2,2×105 |
1,8×105 |
1,6×105 |
2,4×105 |
5 |
Масса одного погонного метра металлоконструкций q |
кг/м |
5×103 |
5×103 |
5×103 |
5×103 |
5×103 |
6 |
Угловая координата звена 1
для силового расчета j1 |
град |
70 |
65 |
75 |
65 |
70 |
7 |
Передаточное отношение зубчатого механизма u16 |
— |
12 |
14 |
18 |
16 |
15 |
8 |
Число сателлитов планетарного редуктора k |
— |
3 |
3 |
3 |
3 |
3 |
9 |
Числа зубьев колес 5 и 6
z5/z6 |
— |
12/18 |
11/22 |
14/21 |
11/22 |
12/18 |
10 |
Модуль m колес z5, z6 |
мм |
8 |
9 |
7 |
9 |
10 |
11 |
Ход толкателя кулачкового механизма hт |
м |
0,01 |
0,015 |
0,008 |
0,01 |
0,013 |

Рис. 144
Задание № 145. Проектирование и исследование
механизмов автомобиля
с гидромеханической трансмиссией
Легковой автомобиль среднего класса оснащен четырехтактным четырехцилиндровым бензиновым двигателем (ДВС) (рис. 145, а) и гидромеханической передачей (ГМП), которая состоит из гидродинамического трансформатора (ГДТ) крутящего момента и планетарной коробки передач (ПКП). Крутящий момент от ГМП к колесам (К) передается с помощью карданного вала (КВ) через главную передачу (ГП) и дифференциал Д.
Основной механизм двигателя состоит из четырех одинаковых кривошипно-ползунных механизмов, расположенных под углом 20° к вертикали на одном коленчатом валу со сдвигом в 180° (рис. 145, б), где 1 - кривошип; 2 - шатун; 3 - поршень; 4 - клапан; 5 - коромысло; 6 - кулачок; 7 - цепная передача. Рабочий цикл в каждом цилиндре двигателя совершается за два оборота коленчатого вала и характеризуется индикаторной диаграммой, данные для построения которой приведены в табл. 145.1. Порядок чередования процессов в цилиндрах двигателя представлен в табл. 145.2.
Управление процессом газораспределения осуществляется клапанами, приводимыми в движение кулачками на распределительном валу, кинематически связанном с коленчатым валом через цепную передачу (см. рис. 145, б). Движение от кулачка на клапан передается посредством качающегося толкателя (коромысла). Закон изменения ускорения клапана соответствует графику на рис. 145, в.
Система смазки двигателя принудительная. Давление в ней создается с помощью шестеренчатого насоса, приводимого от коленчатого вала (на рис. 145 не показан). Гидродинамический трансформатор состоит из насосного колеса Н (см. рис. 145, а), жестко соединенного с маховиком двигателя М, и турбинного колеса Т, закрепленного на входном валу планетарной коробки передач. Полость гидротрансформатора заполнена специальной жидкостью, которая разгоняется лопатками насосного колеса и направляется на лопатки турбинного колеса. При этом происходит увеличение крутящего момента, которое отображается безразмерной характеристикой коэффициента трансформации К = МТ / МН в зависимости от передаточного отношения UГДТ = wT / wH (рис. 145, г).
При проектировании следует считать известными параметры, приведенные в табл. 145.3.
Задание на проектирование:
1. Определить скорость автомобиля на установившемся режиме при постоянном сопротивлении движению.
2. Провести силовой анализ кривошипно-ползунного механизма двигателя за цикл.
3. Спроектировать зубчатую пару масляного насоса двигателя и подобрать числа зубьев z3 , z4 , z5 планетарного ряда в ПКП
(

4. Спроектировать кулачковый механизм привода клапанов двигателя при условии получения минимальных габаритов.
П р и м е ч а н и я:
а) наличие в трансмиссии ГДТ, в котором передача крутящего момента осуществляется посредством жидкости, не позволяет использовать одномассную динамическую модель;
б) крутящий момент на насосном колесе за цикл работы двигателя можно считать постоянным.
Т а б л и ц а 145.1
Данные для построения индикаторной диаграммы
Положение поршня |
S/H |
0 |
0,025 |
0,05 |
0,1 |
0,2 |
0,3 |
0,4 |
0,5 |
0,6 |
0,7 |
0,8 |
0,9 |
1,0 |
|||||||||
Расширение |
0,69 |
1,0 |
0,59 |
0,328 |
0,214 |
0,148 |
0,1 |
0,079 |
0,069 |
0,062 |
0,043 |
0,04 |
|||||||||||
Выпуск |
pi |
0,013 |
|||||||||||||||||||||
Всасывание |
____ pmax |
-0,013 |
|||||||||||||||||||||
Сжатие |
0,626 |
0,36 |
0,26 |
0,13 |
0,061 |
0,024 |
0,013 |
0,009 |
-0,002 |
-0,008 |
-0,01 |
-0,013 |
|||||||||||
Чередование процессов в цилиндрах двигателя
Угол поворота коленчатого вала, град |
1-й цилиндр |
2-й цилиндр |
3-й цилиндр |
4-й цилиндр |
0 - 180 |
Расширение |
Сжатие |
Выпуск |
Всасывание |
180 - 360 |
Выпуск |
Расширение |
Всасывание |
Сжатие |
360 - 540 |
Всасывание |
Выпуск |
Сжатие |
Расширение |
540 - 720 |
Сжатие |
Всасывание |
Расширение |
Выпуск |
Т а б л и ц а 145.3
Исходные данные для проектирования
№ п/п |
Величина |
Еди-ница |
Числовые значения величин для вариантов |
||||
изме-рения |
А |
Б |
В |
Г |
Д |
||
1 |
Средняя скорость поршня VC cp |
м/с |
13,5 |
13,4 |
12,3 |
13,8 |
14,5 |
2 |
Отношение длины шатуна к длине кривошипа lBC/lAB |
— |
3,8 |
4,2 |
3,6 |
3,2 |
4,5 |
3 |
Отношение расстояния от точки В
до центра масс шатуна к длине шатуна lBS2/lBC |
— |
0,26 |
0,3 |
0,3 |
0,3 |
0,3 |
4 |
Диаметр цилиндра d |
м |
0,082 |
0,082 |
0,082 |
0,082 |
0,082 |
5 |
Частота вращения коленчатого вала при номинальной нагрузке w1 |
1/с |
607 |
600 |
550 |
620 |
650 |
6 |
Максимальное давление в цилиндре на заданном режиме движения pmax |
МПа |
1,64 |
1,62 |
1,3 |
1,45 |
1,35 |
7 |
Масса шатуна m2 |
кг |
0,8 |
0,85 |
0,85 |
0,75 |
0,95 |
8 |
Масса поршня m3 |
кг |
0,75 |
0,75 |
0,75 |
0,75 |
0,75 |
9 |
Момент инерции коленчатого вала, маховика и насосного колеса с частью жидкости J1 |
кг×м2 |
0,127 |
0,127 |
0,127 |
0,127 |
0,127 |
10 |
Момент инерции шатуна относительно оси, проходящей через ц. м. шатуна J2S |
кг×м2 |
0,0075 |
0,008 |
0,0075 |
0,007 |
0,008 |
11 |
Передаточное отношение ПКП uпкп |
— |
2,5 |
3,0 |
3,2 |
3,5 |
4,0 |
12 |
Передаточное отношение главной передачи uГП |
— |
4,22 |
4,22 |
4,22 |
4,22 |
4,22 |
13 |
Радиус колеса автомобиля rK |
м |
0,293 |
0,293 |
0,293 |
0,293 |
0,293 |
Окончание табл. 145.3
№ п/п |
Величина |
Еди-ница |
Числовые значения величин для вариантов |
||||
изме-рения |
А |
Б |
В |
Г |
Д |
||
14 |
Суммарная сила сопротивления движению автомобиля, приложенная к ведущим колесам Pсопр |
Н |
2000 |
2500 |
2000 |
2500 |
2000 |
15 |
Коэффициент неравномер-ности вращения коленчатого вала на заданном режиме движения d |
— |
0,05 |
0,0135 |
0,01 |
0,01 |
0,01 |
16 |
Угловая координата кривошипа для силового расчета j1 |
град |
30 |
60 |
120 |
240 |
330 |
17 |
Высота подъема клапана h |
м |
0,009 |
0,01 |
0,008 |
0,009 |
0,01 |
18 |
Координаты взаимного расположения распределительного вала и коромысел клапанов: a b |
м м |
0,036 0,025 |
0,036 0,025 |
0,036 0,025 |
0,036 0,025 |
0,036 0,025 |
19 |
Отношение длин плеч коромысла c1 / c2 |
— |
1 |
1 |
0,7 |
1,5 |
1,75 |
20 |
Максимально допустимый угол давления в кулачковом механизме Jдоп |
град |
30 |
30 |
30 |
45 |
45 |
21 |
Соотношение между ускорениями толкателя g |
— |
3,0 |
3,5 |
3,2 |
3,0 |
3,5 |
22 |
Числа зубьев колес масляного насоса z1=z2 |
— |
8 |
10 |
12 |
8 |
10 |
23 |
Угол наклона линии зуба b |
град |
10 |
15 |
20 |
15 |
10 |
24 |
Модуль m колес z1, z2 |
мм |
3,0 |
3,0 |
3,0 |
5,0 |
5,0 |
25 |
Рабочий угол профиля кулачка dраб |
град |
120 |
140 |
110 |
120 |
120 |
26 |
Радиус сферической части коромысла клапана RЕ |
м |
0,01 |
0,015 |
0,01 |
0,015 |
0,01 |
27 |
Число сателлитов в планетарной коробке передач k |
— |
3 |
3 |
3 |
3 |
3 |

Рис. 145
Задание № 146. Проектирование и исследование
подъемно-уравновешивающего механизма
Подъемно-уравновешивающий механизм (рис. 146, а) предназначен для поворота платформы 1 в вертикальной плоскости на заданный угол amax и удержания ее в этом положении.
В исходном положении платформа горизонтальна. Поворот платформы осуществляется подачей рабочей жидкости от гидронасоса Н шестеренчатого типа в соответствующую полость гидроцилиндра 3 через золотниковый распределитель Р. Гидронасос приводится в движение от двигателя Д, имеющего постоянную частоту вращения nД, через планетарный редуктор Пр с числом сателлитов k=3. Механическая характеристика гидронасоса, т.е. зависимость давления, развиваемого насосом, от расхода рабочей жидкости с учетом предохранительного клапана ПрК приведена на рис. 146, в.
Останов платформы в заданном положении осуществляется с помощью кулачкового механизма, состоящего из кулачка 4, кинематически связанного с коромыслом 1 (w4=w1), и поступательно-движущегося роликового толкателя 5, возвращающего золотниковый распределитель Р в нейтральное положение, при котором обе полости гидроцилиндра заперты.
Допустимый угол давления в кулачковом механизме [J]=30°. Закон изменения аналога ускорения толкателя в зависимости от угла поворота кулачка показан на рис. 146, б. Фазовый угол дальнего выстоя в кулачковом механизме jд.в=90°.
Предохранительный ПрК и переливной ПлК клапаны предназначены для ограничения давления рабочей жидкости в гидросистеме. Клапаны настроены на максимальное давление в гидросистеме pmax.
На рис. 146, г представлены качественные графики изменения перепада давления в полостях гидроцилиндра и относительной скорости поршня при повороте платформы в зависимости от угла ее поворота. В начале поворота движение поршня ускоренное, а перепад давления в полостях гидроцилиндра определяется предохранительным клапаном ПрК. После достижения поршнем скорости V0, при которой расход рабочей жидкости становится равным производительности Q0 гидронасоса, движение поршня - равномерным, а перепад давления в полостях гидроцилиндра определяется силами, действующими на платформу, и ее инерционностью.
После возвращения золотникового распределителя Р в нейтральное положение движение поршня становится замедленным, а перепад давления в полостях гидроцилиндра определяется переливным клапаном ПлК.
Задание на проектирование - в соответствии с учебным планом.
П р и м е ч а н и я.
1. При синтезе рычажного механизма обеспечить угол давления в шарнире В в начале подъема равным нулю.
2. При исследовании движения рычажного механизма ввиду относительной малости углов разгона aр и торможения aт по сравнению с amax соответствующие участки графиков изобразить отдельно с увеличенным масштабом по оси абсцисс.
3. Площадь поршня гидроцилиндра рассчитать из условия гарантированного 10 %-ного превышения движущей силы над приведенной силой сопротивления в любой момент времени.
4. Для проектирования зубчатой передачи принять числа зубьев колес кратными (с округлением) числам зубьев колес, образующих внешнее зацепление в планетарном редукторе. Колеса прямозубые (b = 0). Число зубьев меньшего колеса меньше 15. Модуль m=10 мм.
5. Массами гидроцилиндра и поршня со штоком пренебречь.
Т а б л и ц а 146
Исходные данные для проектирования
№ п/п |
Величина |
Еди-ница |
Числовые значения величин для вариантов |
||||
изме-рения |
А |
Б |
В |
Г |
Д |
||
1 |
Максимальное давление в гидросистеме pmax |
МПа |
16 |
12 |
8 |
12 |
16 |
2 |
Угол поворота платформы amax |
град |
60 |
50 |
40 |
60 |
70 |
3 |
Масса платформы m1 |
кг |
10000 |
8000 |
5000 |
6000 |
8000 |
4 |
Момент инерции платформы J1S |
кг×м2 |
60000 |
50000 |
30000 |
40000 |
40000 |
5 |
Координаты центра масс платформы в опущенном положении (yC=0) ХS1 нач/YS1 нач |
м |
4,0/2,0 |
5,0/2,5 |
6,0/3,0 |
3,0/1,5 |
3,0/1,0 |
6 |
Удельная производительность гидронасоса Q0 |
см3/об |
32 |
32 |
16 |
16 |
32 |
7 |
Частота вращения ротора гидронасоса nН |
об/мин |
2000 |
1400 |
1400 |
2000 |
2000 |
8 |
Ход толкателя кулачкового механизма h |
мм |
5 |
6 |
8 |
10 |
8 |
9 |
Частота вращения вала двигателя nД |
об/мин |
5000 |
4000 |
3000 |
4000 |
5000 |
10 |
Ход поршня H |
м |
0,6 |
0,5 |
0,4 |
0,8 |
0,6 |
11 |
Минимальная длина гидроцилиндра lBC min |
м |
0,8 |
0,6 |
0,5 |
1,0 |
0,8 |
12 |
Фазовые углы удаления и сближения в кулачковом механизме jу / jс |
град |
10/10 |
15/15 |
20/20 |
30/30 |
20/20 |

Рис. 146
Задание № 147. Проектирование и исследование
механизмов транспортного средства
с двигателем внутреннего сгорания
Двухтактный трехцилиндровый двигатель внутреннего сгорания (ДВС) используется в качестве силовой установки малой мощности транспортных средств. На рис. 147, а представлена кинематическая схема ДВС с преобразованием поступательного движения ведущего звена 2 во вращательное движение ведомого звена 1 с помощью механизма кулачкового типа, который состоит из трех одинаковых цилиндров 1, 1¢, 1¢¢, установленных на шестигранной шайбе с центром в точке А, расположенной с эксцентриситетом е относительно оси неподвижной планшайбы 3, и толкателя 2 (поршня).
Цикл движения поршня включает такты расширения и такты сжатия (рис. 147, б).
При подходе поршня 2 к верхней мертвой точке ВМТ (см. рис. 147, а, положение 1) открываются продувочные окна в цилиндре, выпускные клапаны, продукты сгорания удаляются и в цилиндр поступает чистый воздух. После перекрытия продувочных окон и закрытия клапанов (см. рис. 147, б, участок а - b) происходит сжатие воздуха, впрыскивание топлива (участок b - с) и в положении низшей мертвой точки НМТ (см. рис. 147, б, положение 7) происходит воспламенение рабочей смеси (участок с - d), расширение продуктов сгорания и их удаление (участок d - а) завершает рабочий цикл ДВС. Циклограмма работы механизмов ДВС приведена в табл. 147.1.
Данные для построения индикаторной диаграммы представлены в табл. 147.2.
На главном валу машинного агрегата (вал А, рис. 147, в) установлен кулачок 4, тарельчатый толкатель 10 которого соединен с диафрагмой топливного насоса. Закон движения толкателя показан на рис. 147, г.
Передача движения на звено 9 транспортного средства (рис. 147, д) осуществляется через одноступенчатую прямозубую эвольвентную цилиндрическую передачу 5 (z1/ z2), однорядный планетарный редуктор 6, карданный вал 7 и коническую передачу 8 (Uкон=1).
Задание на проектирование - в соответствии с учебным планом.
П р и м е ч а н и е.
1. При определении размеров основного механизма ДВС принять размер ступицы шайбы А равным dА = 1,2d, расстояние l*= 0,2H. Центры масс цилиндра и поршня находятся на середине их длин.
2. При определении закона движения главного вала машинного агрегата можно воспользоваться упрощенной расчетной схемой основного механизма (рис. 147, е) и следующими зависимостями:
текущий радиус - вектор точки контакта поршня с планшайбой:

где

Знаки в формуле: « - » при 90°< j1 < 270° ,
« + » при j1 < 90° и j1 > 270° ,
y=x tg(j1).
Движущий момент: Мдв = F t r(j1 ) ,
где F t = F tg(a) = 0,25 p d 2 p(j1) tg(a);

3. При определении закона движения машинного агрегата (МА) для установившегося режима его работы принять, что частота вращения вала A составляет nA=60 1/с, а коэффициент неравномерности d=1/60.
При определении закона движения МА при неустановившемся режиме его работы принять, что в начальный момент времени (j1нач =0, w1нач =0) на звено 1 действует момент запуска


Таблица 147.1
Циклограмма работы механизмов ДВС
Рабочие |
Угол поворота j1, град |
|||
процессы |
0 180 360 |
|||
Такты работы ДВС |
Впрыскивание топлива, сжатие |
Расширение, выхлоп |
||
Фазы движения толкателя |
Сближение |
Ближнее стояние |
Удаление |
Дальнее стояние |
Данные для построения индикаторной диаграммы
Относительное перемещение поршня |
S / H |
0 |
0,05 |
0,1 |
0,2 |
0,3 |
0,4 |
0,5 |
0,6 |
0,7 |
0,8 |
0,9 |
1,0 |
Впрыскивание топлива, сжатие |
pi/pmax |
0,8 |
0,4 |
0,28 |
0,14 |
0,07 |
0,04 |
0,02 |
0,01 |
0 |
0 |
0 |
0 |
Расширение, выхлоп |
0,8 |
1,0 |
0,9 |
0,62 |
0,42 |
0,28 |
0,21 |
0,17 |
0,15 |
0,13 |
0,1 |
0 |
Исходные данные для проектирования
№ п/п |
Величина |
Еди-ница |
Числовые значения величин для вариантов |
||||
изме-рения |
А |
Б |
В |
Г |
Д |
||
1 |
Ход поршня Н |
м |
0,02 |
0,035 |
0,04 |
0,055 |
0,06 |
2 |
Относительный диаметр цилиндра d/h |
— |
1,1 |
1,15 |
1,2 |
1,25 |
1,25 |
3 |
Относительная длина поршня l2=l2 / h |
— |
1,65 |
1,7 |
1,8 |
1,82 |
1,85 |
4 |
Максимальное давление в цилиндре двигателя pmax |
МПа |
2,8 |
3,1 |
3,4 |
3,8 |
3,9 |
5 |
Массы звеньев: - цилиндра m1; - поршня m2 |
кг кг |
1,2 0,8 |
1,4 0,9 |
1,5 1,0 |
1,6 1,1 |
1,7 1,3 |
6 |
Момент инерции: зубчатого колеса z1, Jz1 зубчатого колеса z2, Jz2 |
кг×м2 кг×м2 |
0,001 0,003 |
0,002 0,004 |
0,003 0,005 |
0,004 0,006 |
0,005 0,007 |
7 |
Приведенный к валу В момент инерции вращающихся звеньев планетарной передачи ![]() |
кг×м2 |
0,03 |
0,04 |
0,05 |
0,06 |
0,07 |
Окончание табл. 147.3
№ п/п |
Величина |
Еди-ница |
Числовые значения величин для вариантов |
||||
изме-рения |
А |
Б |
В |
Г |
Д |
||
8 |
Приведенный к валу A момент инерции звеньев кулачкового механизма ![]() |
кг×м2 |
0,004 |
0,005 |
0,006 |
0,007 |
0,008 |
9 |
Передаточное отношение между валом А и карданным валом uобщ |
— |
14 |
9 |
15 |
12 |
7 |
10 |
Числа зубьев колес z1 /z2 |
— |
18/30 |
11/24 |
21/34 |
16/28 |
12/26 |
11 |
Модуль зубчатых колес m |
мм |
2,0 |
3,5 |
2,5 |
3,0 |
4,0 |
12 |
Число сателлитов планетарного редуктора k |
— |
3 |
3 |
3 |
3 |
3 |
13 |
Максимальный ход толкателя кулачкового механизма h |
мм |
6 |
8 |
9 |
10 |
12 |
14 |
Фазовые углы кулачкового механизма: - угол удаления jу; - угол дальнего стояния jдс; - угол сближения jс |
град град град |
104 56 130 |
115 40 125 |
120 45 115 |
130 30 110 |
140 15 105 |
15 |
Угловая координата вала А для силового расчета j1 |
град |
190 |
200 |
210 |
220 |
230 |
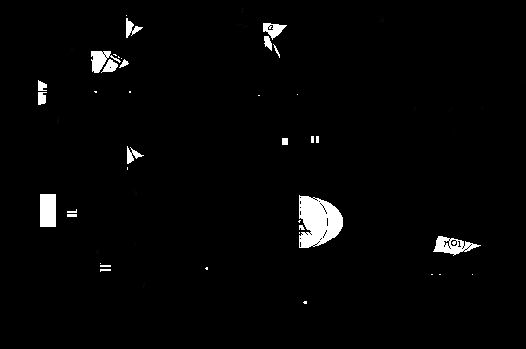
Рис. 147
Задание № 148. Исследование и проектирование
механизмов двухступенчатого поршневого
компрессора
Двухступенчатый поршневой компрессор предназначен для наполнения баллонов воздухом. Наполнение осуществляется следующим образом. При достижении максимального давления в цилиндре первой ступени сжатый воздух через ресивер-охладитель (на рис. 148 не показан) поступает в цилиндр второй ступени, затем при достижении максимального давления в цилиндре второй ступени сжатый воздух нагнетается в баллон.
Двухступенчатый поршневой компрессор (рис. 148, а) приводится в движение от электродвигателя 7. Вал электродвигателя связан с коленчатым валом компрессора посредством муфты 8. Режим работы механизма - установившийся.
Основным механизмом компрессора является кривошипно-ползунный механизм (рис. 148, б), состоящий из коленчатого вала 1, шатунов 2 и 4, поршней 3 и 5, перемещающихся в цилиндрах.
Все расчетные данные в соответствии с вариантом курсового проекта приведены в табл. 148.1. Изменение давления в цилиндрах в зависимости от положения поршня представлено на индикаторных диаграммах (рис. 148, в и г), данные для построения которых приведены в табл. 148.2 и 148.3.
Для расчета зубчатой передачи, планетарного редуктора и кулачкового механизма использовать данные, приведенные в других заданиях (по рекомендации преподавателя).
Задание на проектирование дано в соответствии с учебным планом.
Т а б л и ц а 148.1
Исходные данные для проектирования
№ п/п |
Величина |
Еди-ница |
Числовые значения величин для вариантов |
||||
изме-рения |
А |
Б |
В |
Г |
Д |
||
1 |
Отношение длины шатуна к длине кривошипа l2 = l4 |
— |
5 |
5,2 |
4,5 |
5 |
5,4 |
2 |
Отношение расстояний от точки В до центров масс шатунов к длине шатунов lS2 = = lS4 |
— |
0,3 |
0,3 |
0,3 |
0,3 |
0,3 |
3 |
Частота вращения коленчатого вала n1 |
об ____ мин |
1430 |
1500 |
1450 |
1550 |
1400 |
4 |
Средняя скорость поршня Vср |
м/с |
5,7 |
5,8 |
5,7 |
5,8 |
5,7 |
5 |
Максимальное давление воздуха в цилиндре первой ступени pmax I |
кПа |
200 |
206,5 |
210 |
180 |
190 |
6 |
Максимальное давление воздуха в цилиндре второй ступени pmax II |
кПа |
600 |
620 |
630 |
540 |
570 |
7 |
Массы шатунов m2,4 |
кг |
8 |
7 |
8 |
7,5 |
8 |
8 |
Массы поршней m3,5 |
кг |
10 |
10,5 |
11 |
10 |
10,2 |
9 |
Моменты инерции шатунов относительно осей, проходящих через их центры масс JS2 = JS4 |
кг×м2 |
0,022 |
0,022 |
0,023 |
0,024 |
0,025 |
10 |
Момент инерции коленчатого вала и вращающихся звеньев, приведенных к валу звена 1
![]() |
кг×м2 |
0,273 |
0,273 |
0,273 |
0,273 |
0,273 |
11 |
Коэффициент неравномерности вращения коленчатого вала d |
— |
0,01 |
0,01 |
0,015 |
0,012 |
0,01 |
12 |
Угловая координата кривошипа для силового расчета j1 |
град |
60 |
70 |
65 |
45 |
60 |
13 |
Диаметр цилиндра первой ступени d3 |
м |
0,21 |
0,20 |
0,22 |
0,21 |
0,22 |
14 |
Диаметр цилиндра второй ступени d5 |
м |
0,125 |
0,120 |
0,122 |
0,124 |
0,125 |
Т а б л и ц а 148.2
Данные для построения индикаторной диаграммы (ступень I)
Путь поршня (в долях хода H) |
![]() |
0,0 |
0,1 |
0,2 |
0,3 |
0,4 |
0,5 |
0,6 |
0,7 |
0,8 |
0,9 |
1,0 |
Сжатие, нагнетание |
![]() |
0,75 |
1,0 |
1,0 |
1,0 |
0,75 |
0,50 |
0,35 |
0,15 |
0,0 |
-0,001 |
-0,013 |
Расширение, всасывание |
![]() |
0,75 |
-0,019 |
-0,024 |
-0,024 |
-0,024 |
-0,023 |
-0,022 |
-0,021 |
-0,020 |
-0,019 |
-0,013 |
Данные для построения индикаторной диаграммы (ступень II)
Путь поршня (в долях хода H) |
![]() |
0,0 |
0,1 |
0,2 |
0,3 |
0,4 |
0,5 |
0,6 |
0,7 |
0,8 |
0,9 |
1,0 |
Сжатие, нагнетание |
![]() |
0,76 |
1,0 |
0,94 |
0,83 |
0,71 |
0,60 |
0,48 |
0,43 |
0,38 |
0,35 |
0,34 |
Расширение, всасывание |
![]() |
0,76 |
0,43 |
0,38 |
0,333 |
0,333 |
0,333 |
0,333 |
0,333 |
0,333 |
0,333 |
0,34 |

Рис. 148
Задание № 149. Проектирование и исследование
механизмов двигателя типа «ш»
Двигатель внутреннего сгорания (ДВС) трехцилиндровый типа Ш [2] показан на рис. 149, а. Основной механизм двигателя состоит из трех одинаковых кривошипно-ползунных механизмов. Шатуны 2, 4 и 6 присоединены к общему кривошипу 1. Развал осей цилиндров I, II и II, III равен 60°.
Потребитель энергии - компрессор передвижной холодильной установки - подсоединяется к главному валу двигателя - кривошипу 1, через муфту 14 и однорядный планетарный редуктор 15 с передаточным отношением U1H и числом сателлитов k = 3 (рис. 149, б).
На коленчатом валу 1 установлен маховик 13, обеспечивающий колебания угловой скорости с заданным коэффициентом неравномерности d.
Двигатель четырехтактный и рабочие процессы в цилиндрах двигателя протекают за два полных оборота кривошипа 1. Характер изменения давления в цилиндрах по ходу поршня представлен индикаторной диаграммой двигателя, данные для построения которой приведены в табл. 149.1. Последовательность протекания рабочих процессов в цилиндрах показана в табл. 149.2.
Перемещение клапанов двигателя осуществляется одинаковыми кулачковыми механизмами 10 - 12. Кулачок приводится в движение зубчатой передачей 8 - 9 с модулем m=5 мм и углом наклона линии зуба b = 0 от коленчатого вала 1. Закон изменения тангенциального ускорения атt толкателя выбирают по согласованию с преподавателем. Максимально допустимый угол давления в кулачковом механизме [J]=28°.
Задание на проектирование - в соответствии с учебным планом.
Т а б л и ц а 149.1
Значения давления в цилиндре двигателя в долях максимального давления pmax в зависимости от положения поршня
Ход поршня (в долях хода H) |
![]() |
0 |
0,025 |
0,05 |
0,1 |
0,2 |
0,3 |
0,4 |
0,5 |
0,6 |
0,7 |
0,8 |
0,9 |
1 |
Расширение |
0,4 |
1 |
0,96 |
0,83 |
0,62 |
0,46 |
0,36 |
0,28 |
0,22 |
0,19 |
0,15 |
0,12 |
0,094 |
|
Выхлоп |
pi __ |
0,005 |
0,005 |
0,005 |
0,005 |
0,005 |
0,005 |
0,005 |
0,005 |
0,005 |
0,005 |
0,005 |
0,005 |
0,094 |
Всасывание |
pmax |
0,005 |
0 |
-0,006 |
-0,006 |
-0,006 |
-0,006 |
-0,006 |
-0,006 |
-0,006 |
-0,006 |
-0,006 |
-0,006 |
-0,006 |
Сжатие |
0,4 |
0,28 |
0,26 |
0,2 |
0,11 |
0,069 |
0,046 |
0,03 |
0,014 |
0 |
-0,0014 |
-0,003 |
-0,006 |
Чередование процессов в цилиндрах двигателя
Ци- |
Порядковый номер положения кривошипа 1 |
|||||||||||||||||||||||||||||||||||
линдр |
0 |
1 |
2 |
3 |
4 |
5 |
6 |
7 |
8 |
9 |
10 |
11 |
12 |
1 |
2 |
3 |
4 |
5 |
6 |
7 |
8 |
9 |
10 |
11 |
12 |
|||||||||||
I |
Всасывание |
Сжатие |
Расширение |
Выхлоп |
Всасывание |
|||||||||||||||||||||||||||||||
II |
Расширение |
Выхлоп |
Всасывание |
Сжатие |
||||||||||||||||||||||||||||||||
III |
Выхлоп |
Всасывание |
Сжатие |
Расширение |
Выхлоп |
|||||||||||||||||||||||||||||||
Т а б л и ц а 149.3
Исходные данные для проектирования
№ п/п |
Величина |
Еди-ница |
Числовые значения величин для вариантов |
||||
изме-рения |
А |
Б |
В |
Г |
Д |
||
1 |
Средняя скорость порш-ня двигателя
Vср |
м/с |
1,6 |
1,8 |
1,5 |
1,2 |
1,4 |
2 |
Диаметр цилиндров d |
м |
0,11 |
0,1 |
0,105 |
0,099 |
0,107 |
3 |
Ход поршня H |
м |
0,25 |
0,22 |
0,25 |
0,3 |
0,2 |
4 |
Отношение длины шатуна к длине кривошипа l2=lBC / lAB |
___ |
3,6 |
4 |
3,5 |
3,2 |
4,5 |
5 |
Относительное положение центра масс шатуна l3=lBS2 / lBC |
___ |
0,25 |
0,27 |
0,3 |
0,28 |
0,31 |
6 |
Максимальное давление в цилиндрах двигателя pmax |
МПа |
7 |
6,8 |
7,2 |
6,95 |
7,25 |
7 |
Масса шатуна m2=m4= =m6 |
кг |
1,95 |
1,77 |
1,85 |
1,75 |
1,90 |
8 |
Масса поршня m3=m5= =m7 |
кг |
9,75 |
8,85 |
9,30 |
8,75 |
9,45 |
9 |
Момент инерции шатуна относительно оси, проходящей через центр масс JS2= JS4=
JS6 |
кг×м2 |
0,033 |
0,037 |
0,030 |
0,023 |
0,050 |
10 |
Приведенный к валу двигателя момент инерции вращающихся деталей привода ![]() |
кг×м2 |
3,1 |
3,05 |
3,1 |
3,2 |
3 |
11 |
Коэффициент неравномерности вращения вала 1 d |
¾ |
0,025 |
0,028 |
0,03 |
0,02 |
0,022 |
12 |
Угловая координата зве-на 1
для силового расчета j1 |
град |
30 |
330 |
90 |
450 |
45 |
13 |
Угол рабочего профиля кулачка jр |
град |
180 |
170 |
180 |
190 |
180 |
14 |
Ход толкателя hт |
м |
0,011 |
0,01 |
0,014 |
0,012 |
0,015 |
15 |
Число зубьев колес 8 и 9 z8 /z9 |
¾ |
11/22 |
12/24 |
10/20 |
11/22 |
14/28 |
16 |
Передаточное отношение планетарного редуктора U1H |
¾ |
4,5 |
3,6 |
4 |
4,1 |
4,3 |

Рис. 149
Задание № 150. Проектирование и исследование
механизмов ДВС-насосной установки
ДВС-насосная (ДВС - двигатель внутреннего сгорания) установка [3] представляет собой V-образную поршневую машину, у которой развал осей цилиндров I и II равен 60° (рис. 150, а). Она состоит из двух кривошипно-ползунных механизмов, причем кривошипы 1 и 1¢, шатуны 2 и 4 одинаковы, а поршни 3 и 5 имеют различные диаметры: диаметр цилиндра I ДВС равен d3, диаметр цилиндра II насоса - d5.
Движение передается от ДВС через муфту М (рис. 150, б) на коленчатый вал насоса 1¢. Для обеспечения заданной амплитуды колебаний угловой скорости на коленчатом валу двигателя 1 установлен маховик МАХ, обеспечивающий заданный коэффициент неравномерности d.
Рабочие процессы в цилиндрах I и II двухтактные. Последовательность чередования рабочих процессов в цилиндрах представлена в табл. 150.1. Характер изменения давления в цилиндре по ходу поршня 3 представлен индикаторной диаграммой ДВС, данные для построения которой приведены в табл. 150.2. В цилиндре II на этапе нагнетания


Максимальное давление в цилиндре двигателя



Перемещение впускного клапана двигателя осуществляется кулачковым механизмом 8 - 9. Кулачок приводится в движение посредством зубчатой передачи 6 - 7 - 6¢ от коленчатого вала 1 (угол наклона линии зуба b = 0). Закон изменения тангенциального ускорения аt толкателя в зависимости от угла поворота кулачка представлен на рис. 150, в.
Проектирование планетарного редуктора выполнить по согласованию с преподавателем.
Задание на проектирование - в соответствии с учебным планом.
П р и м е ч а н и я.
1. Определение закона движения при установившемся режиме работы ДВС-насосной установки выполнить, когда сцепная муфта М подсоединяет вал насоса в положении, показанном на рис. 150, а.
2. Коэффициенты полезного действия (КПД) двигателя и насоса
hд = hн = 1. При решении усложненного варианта задания рекомендуется принять КПД: двигателя hд=0,4; насоса hн =0,5.
Т а б л и ц а 150.1
Чередование процессов в цилиндрах двигателя и насоса
Цилиндр |
Порядковый номер положения кривошипа 1 |
||||||||||||||
0 |
1 |
2 |
3 |
4 |
5 |
6 |
7 |
8 |
9 |
10 |
11 |
12 |
|||
Двигатель |
Расширение/Выхлоп |
Всасывание/Сжатие |
|||||||||||||
Насос |
Нагнетание |
Всасывание |
|||||||||||||
Значения давления в цилиндре двигателя
Путь поршня (в долях хода H) |
![]() |
0 |
0,03 |
0,05 |
0,1 |
0,2 |
0,3 |
0,4 |
0,5 |
0,6 |
0,7 |
0,8 |
0,9 |
1,0 |
Расширение |
pi ___ |
0,6 |
1 |
0,9 |
0,7 |
0,49 |
0,38 |
0,29 |
0,23 |
0,19 |
0,16 |
0,13 |
0,09 |
0,02 |
Сжатие |
pmax д |
0,6 |
0,45 |
0,39 |
0,3 |
0,19 |
0,13 |
0,08 |
0,06 |
0,02 |
0,015 |
0,01 |
0,015 |
0,02 |
Т а б л и ц а 150.3
Исходные данные для проектирования
№ п/п |
Величина |
Еди-ница |
Числовые значения величин для вариантов |
||||
изме-рения |
А |
Б |
В |
Г |
Д |
||
1 |
Средняя скорость поршня двигателя Vср |
м/с |
1,5 |
1,6 |
1,4 |
1,8 |
1,4 |
2 |
Диаметр цилиндра 3 d3 |
м |
0,115 |
0,095 |
0,102 |
0,125 |
0,117 |
3 |
Диаметр цилиндра 5 d5 |
м |
0,095 |
0,08 |
0,08 |
0,092 |
0,088 |
4 |
Ход поршня H |
м |
0,24 |
0,2 |
0,25 |
0,28 |
0,3 |
5 |
Отношение длины шатуна к длине кривошипа l2=lBC / lAB |
___ |
3,8 |
3,4 |
4,3 |
4,1 |
3,7 |
6 |
Относительное положение центра масс шатуна l3= =lBS2 / lBC |
___ |
0,26 |
0,31 |
0,34 |
0,28 |
0,29 |
7 |
Коэффициент a |
¾ |
4,66 |
4,61 |
4,70 |
4,68 |
4,65 |
8 |
Максимальное давление в цилиндре насоса pmax н |
МПа |
0,45 |
0,42 |
0,5 |
0,62 |
0,58 |
9 |
Масса кривошипа m1 |
кг |
1,13 |
0,93 |
0,84 |
1,08 |
1,12 |
10 |
Масса шатуна m2=m4 |
кг |
2,04 |
1,67 |
1,80 |
2,23 |
2,08 |
11 |
Масса поршня двигателя m3 |
кг |
10,2 |
8,37 |
9,01 |
11,13 |
10,4 |
12 |
Масса поршня насоса m5 |
кг |
8,37 |
7,01 |
7,01 |
8,10 |
7,74 |
13 |
Момент инерции шатуна от-носительно оси, проходящей через центр масс JS2=JS4 |
кг×м2 |
0,038 |
0,025 |
0,043 |
0,05 |
0,037 |
14 |
Момент инерции вращаю-щихся деталей, приведенный к валу кривошипа ![]() |
кг×м2 |
0,160 |
0,080 |
0,120 |
0,300 |
0,335 |
15 |
Коэффициент неравномерности вращения вала 1 d |
¾ |
0,026 |
0,02 |
0,025 |
0,03 |
0,028 |
16 |
Угловая координата звена 1 для силового расчета j1 |
град |
60 |
30 |
45 |
15 |
20 |
17 |
Угол рабочего профиля кулачка j8р |
град |
70 |
80 |
80 |
75 |
70 |
18 |
Ход толкателя hт |
м |
0,015 |
0,017 |
0,015 |
0,011 |
0,014 |
19 |
Максимально допустимый угол давления в кулачковом механизме [J] |
град |
25 |
28 |
28 |
30 |
28 |
20 |
Число зубьев колес 6 и 7
z6/z7 |
¾ |
13/39 |
11/22 |
11/33 |
14/24 |
10/30 |
21 |
Модуль зубчатых колес m6,7 |
мм |
5 |
6 |
6 |
5 |
5 |

Рис. 150
Задание № 151. Опорное устройство
Опорное устройство служит для установки изделия перед использованием.
Изделие устанавливают на шесть автономных опор, гидравлически связанных между собой, что обеспечивает синхронность их срабатывания.
Структурная схема одной опоры (рис. 151, а) представляет собой плоский семизвенный рычажный механизм, имеющий в своем составе механизм шарнирного параллелограмма ABCD. Размеры звеньев определяются соотношениями:
lAB = lCD = 2,8 м; lAD = lBC = 0,6 м; lBE = 1,6 м; lOK = 4,0 м; lOM = 5,0 м.
Координаты опорных шарниров:
xA = 0; yA = 0; xD = xO = 0; yO = - 5,1 м; xU = - 4,8 м; yU = - 7,2 .
Воздействие изделия на опору определяется силой FM, изменяющейся по закону, представленному на рис. 151, б.
Механизм опоры фиксируется под нагрузкой дополнительным устройством (на рисунке не показано), при этом угловая координата звена 1 в начальном положении опоры j1 нач =150°. При сходе изделия опора освобождается; отвод опоры осуществляется под воздействием противовеса, установленного на звене 2. Угловая координата звена 1 в конечном положении опоры j1 кон =210°.
Торможение опоры осуществляется с помощью гидравлического буфера, с момента, когда j1 = j1 ГБ, обеспечивая ее безударный останов.
При установке опоры в исходное положение используется зубчатый механизм, состоящий из однорядного планетарного редуктора с числами зубьев z1, z2, z3 (рис. 151, в) и зубчатой передачи с числами зубьев колес z4, z5. Передаточное отношение зубчатого механизма U15. Угол наклона линии зуба зубчатых колес b = 0.
Смазка подвижных соединений опор осуществляется с помощью масляного насоса кулачкового типа (рис. 151, г), состоящего из дискового кулачка 8 и роликового толкателя 9. Закон изменения ускорения толкателя в зависимости от угла поворота кулачка представлен на рис. 151, г.
Задание на проектирование - в соответствии с учебным планом.
П р и м е ч а н и я:
1. Проектирование кинематической схемы рычажного механизма следует выполнять из условия, что в конечный момент работы механизма, т.
е. при j1= j1 кон, угловая координата звена 5 j5=180° (см. рис. 151, а).
2. При определении закона движения механизма расчеты проводить с интервалом изменения угловой координаты звена 1 Dj1 = 5°.
3. Учет трения в кинематических парах механизма выполнить условно, считая суммарный приведенный момент от сил трения постоянным и равным


4. Приведенный момент от силы сопротивления гидробуфера принять постоянным в течение всего периода работы гидробуфера.
5. Центры масс звеньев рычажного механизма расположены посередине длин звеньев. Массу противовеса считать сосредоточенной в точке S2 (xS2 нач =xU; yS2 нач =yB).
Массы звеньев определять по соотношению mi = qi li.
6. Моменты инерции звеньев относительно осей, проходящих через центры масс звеньев, рассчитать по формуле

7. При проектировании рабочего профиля кулачка угловую скорость кулачка принять постоянной и численно равной w8 = 5w1 max. Допустимый угол давления [J] = 30°.
Т а б л и ц а 151
Исходные данные для проектирования
№ п/п |
Величина |
Еди-ница |
Числовые значения величин для вариантов |
||||
изме-рения |
А |
Б |
В |
Г |
Д |
||
1 |
Угловая координата звена 1, соответствующая моменту окончательного схода изделия с опоры j1 F |
град |
160 |
160 |
160 |
160 |
155 |
2 |
Угловая координата звена 1, соответствующая моменту начала работы гидробуфера j1 ГБ |
град |
180 |
180 |
180 |
195 |
180 |
Окончание табл. 151
№ п/п |
Величина |
Еди-ница |
Числовые значения величин для вариантов |
||||
изме-рения |
А |
Б |
В |
Г |
Д |
||
3 |
Максимальное значение силы FM max |
Н |
1,2×106 |
1,4×106 |
1,1×106 |
106 |
1,4×106 |
4 |
Масса противовеса m2 |
кг |
1,4×105 |
1,65×105 |
1,3×105 |
1,2×105 |
1,63×105 |
5 |
Масса одного погонного метра металлоконструк-ций q |
кг/м |
4×103 |
4×103 |
4×103 |
4×103 |
4×103 |
6 |
Угловая координата звена 1 для силового расчета j1 |
град |
170 |
165 |
175 |
180 |
175 |
7 |
Передаточные отношения зубчатого механизма u15 |
— |
10 |
6 |
9 |
5 |
8 |
8 |
Число сателлитов планетарного редуктора k |
— |
3 |
3 |
3 |
3 |
3 |
9 |
Числа зубьев колес 4, 5 z4/z5 |
— |
11/22 |
12/18 |
14/21 |
12/20 |
12/16 |
10 |
Модуль колес m |
мм |
8 |
10 |
12 |
14 |
10 |
11 |
Ход толкателя кулачкового механизма hТ |
м |
0,02 |
0,015 |
0,015 |
0,01 |
0,01 |
12 |
Угол рабочего профиля кулачка dp |
град |
220 |
200 |
210 |
190 |
200 |

Рис. 151
Приложение
Пояснения к заданиям № 106 и 150
В заданиях 106 и 150 необходимо определить максимальное давление в цилиндре двигателя, зная давление в цилиндре насоса (или компрессора).
Закон движения механизма определяют для установившегося режима, при котором работа движущих сил равна работе сил сопротивления за цикл работы установки. С учетом коэффициентов полезного действия (КПД) механизмов, входящих в установку, условие равенства работ примет вид


где hS = hд×hс - КПД машинного агрегата; hд - КПД двигателя; hс - КПД насоса (компрессора).
Определим работу сил сопротивления. В исходных данных заданы значения давления в цилиндре насоса (компрессора) как зависимость относительного давления bci= pci /pmax c в долях от хода поршня S/H.
Для определения значения давления в рабочей полости цилиндра в каждом положении поршня следует домножить относительное давление на максимальное давление pmax c в насосе (компрес-соре):

Сила сопротивления определяется как произведение давления
pci на площадь поршня насоса (компрессора):

где dс - диаметр поршня насоса (компрессора).
Приведенный момент сопротивления определим из условия равенства элементарных работ действительных сил и приведенного момента на возможных перемещениях звеньев их приложения:

или

где Vqc и

Работа сил сопротивления за цикл равна интегралу от приведенного момента сопротивления по углу поворота звена приведения j1 (рад) в пределах от его начального



Теперь определим работу движущих сил за цикл. Значения относительного давления bдi= pдi /pmax д в цилиндре двигателя заданы в табличном виде в зависимости от хода поршня.
Аналогично работе сил сопротивления работу движущих сил за цикл выразим зависимостью

где dд - диаметр поршня двигателя, Vqд и

Как уже говорилось выше, при установившемся движении имеет место равенство работ движущих сил и сил сопротивления за цикл:

или

Из последнего равенства определяем неизвестное значение максимального давления в двигателе pmax д:

где

Заменяя интеграл суммой, получаем

где n - число позиций механизма. Часто принимают Dj1i=Dj1=2p/n для двухтактного ДВС или Dj1i=Dj1=4p/n для четырехтактного ДВС.
Коэффициент a обычно находят численным методом.
Список литературы
1. Попов С.А., Тимофеев Г.А. Курсовое проектирование по теории механизмов и механике машин. - М.: Высш. шк., 1998.
2. Михайлов А.К., Ворошилов В.П. Компрессорные машины: Учеб. для вузов. - М.: Энергоатомиздат, 1989.
3. Васильченко В.А. Гидравлическое оборудование мобильных машин: Справ. - М.: Машиностроение, 1983.
Содержание
Задание № 143. Проектирование механизмов трехподвижного уравновешенного манипулятора .......................... 3
Задание № 144. Проектирование и исследование механизма опор-
ного устройства ..................................................... 8
Задание № 145. Проектирование и исследование механизмов ав-томобиля с гидромеханической трансмиссией...... 12
Задание № 146. Проектирование и исследование подъемно-урав-новешивающего механизма .................................. 17
Задание № 147. Проектирование и исследование механизмов транспортного средства с двигателем внутреннего сгорания ................................................................. 20
Задание № 148. Исследование и проектирование механизмов двухступенчатого поршневого компрессора........ 25
Задание № 149. Проектирование и исследование механизмов дви-гателя типа «ш»..................................................... 29
Задание № 150. Проектирование и исследование механизмов ДВС-насосной установки ..................................... 33
Задание № 151. Опорное устройство .............................................. 37
Приложение .................................................................................... 41Список литературы ......................................................................... 43
* Нумерация заданий в сборнике продолжает нумерацию в предыдущих сборниках